views
Enameled Flat Wire: Design, Properties, and Industrial Applications
In the evolving world of electrical engineering and manufacturing, the demand for compact, efficient, and high-performance components is constantly rising. One of the critical components that have emerged to meet these demands is Enameled Flat Wire—a specialized type of magnet wire used extensively in electrical motors, transformers, inductors, and other electromagnetic devices.
Enameled flat wire combines the electrical performance of conductive metal with space-saving geometry and thermal-resistant insulation, making it ideal for high-density winding applications.
What Is Enameled Flat Wire?
Enameled flat wire, also known as rectangular magnet wire or flat magnet wire, is a conductive wire with a rectangular or square cross-section, coated with a thin layer of insulating enamel. This enamel serves as an electrical insulator and can withstand high temperatures and harsh operating environments.
The conductor is typically copper or aluminum, chosen for its electrical conductivity and mechanical properties. The enamel insulation can consist of one or more layers of materials such as:
-
Polyester
-
Polyimide
-
Polyamide-imide
-
Polyurethane
-
Glass-fiber-reinforced coatings
The insulation class is typically rated according to international standards like IEC 60317, NEMA MW1000, or JIS C3202, and the thermal class can range from 130°C to over 240°C, depending on application needs.
Key Features and Advantages
1. Space Efficiency
Flat wire provides better space utilization compared to round wire because the coils can be wound more tightly. This is especially important in applications like electric vehicle (EV) motors and transformers where compact design and high power density are crucial.
2. Improved Heat Dissipation
The flat geometry increases the surface area relative to volume, enhancing heat dissipation. This allows devices using flat wire to operate at higher power levels without overheating.
3. Higher Filling Factor
The slot filling factor—the ratio of copper to insulation and voids in the winding area—is higher in flat wire compared to round wire. This leads to improved efficiency and lower electrical losses in motors and transformers.
4. Mechanical Strength
Flat wire offers better mechanical stability, making it less prone to movement or vibration in high-speed motors and reducing the risk of insulation damage.
5. High-Frequency Performance
In high-frequency applications, enameled flat wire reduces eddy current and skin effect losses compared to thick round wire, particularly when multiple thin flat wires are used in parallel (e.g., Litz wire configuration).
Manufacturing Process
The production of enameled flat wire involves several precise steps:
-
Wire Drawing: The base metal (typically copper or aluminum) is drawn into a rectangular cross-section through specialized dies.
-
Annealing: The drawn wire is heat-treated to remove stresses and improve ductility.
-
Enameling: The wire passes through multiple coating stages where enamel is applied and cured using heat.
-
Quality Testing: The final product is tested for insulation integrity, conductor dimensions, dielectric strength, and thermal resistance.
Applications of Enameled Flat Wire
Enameled flat wire is used in a wide variety of demanding applications where high performance, compact size, and thermal endurance are critical.
1. Electric Motors
Used extensively in high-efficiency motors for electric vehicles, drones, and industrial automation. The flat geometry allows more copper in the slot, increasing torque density.
2. Transformers
Ideal for high-frequency and high-power transformers, such as those used in switch-mode power supplies (SMPS) and energy storage systems.
3. Inductors and Chokes
Flat wire allows better winding and thermal performance in components where energy storage and conversion efficiency are critical.
4. Wireless Charging Coils
Thin, closely wound flat wire improves magnetic coupling and minimizes energy loss in wireless power transfer systems.
5. Wind Turbines and Generators
Used in the stator windings for large-scale generators due to improved slot utilization and mechanical stability.
Comparison: Enameled Flat Wire vs Enameled Round Wire
Types of Enameled Flat Wire
Based on Material:
-
Copper Flat Wire: Offers best conductivity, widely used in precision electronics and EV motors.
-
Aluminum Flat Wire: Lighter and cheaper, commonly used in large transformers and coils where weight matters.
Based on Insulation:
-
Single Coat Enamel: Suitable for standard conditions.
-
Double/Triple Coat Enamel: Provides higher dielectric strength and temperature resistance.
-
Self-Bonding Flat Wire: Has a bondable topcoat that enables winding without external adhesives.
-
Glass-Fiber-Coated Flat Wire: Used in high-voltage, high-temperature environments.
Industry Standards and Specifications
Common international standards covering enameled flat wire include:
-
IEC 60317: Specifications for different types of enamel insulation.
-
NEMA MW 1000: U.S. standard for magnet wires.
-
JIS C3202: Japanese standards for wire diameter, insulation, and performance.
Manufacturers may also offer custom sizes, thermal ratings, and specialty coatings based on client requirements.
Challenges and Considerations
While enameled flat wire offers numerous benefits, it also introduces challenges:
-
Winding Complexity: Special winding machines are required due to the rigid shape and need for precise layering.
-
Bending Radius: Flat wires are more prone to cracking if bent sharply.
-
Cost: Processing and material costs are higher than for round wire.
-
Availability: Custom sizes or coatings may require long lead times.
Conclusion
Enameled flat wire is a critical advancement in the field of electrical windings, providing unmatched performance in compact, high-efficiency systems. Its ability to optimize space, improve heat dissipation, and enhance mechanical and thermal reliability makes it the preferred choice in modern motors, transformers, and high-frequency applications.
As industries move toward electrification and miniaturization—particularly in sectors like electric vehicles, renewable energy, and industrial automation—enameled flat wire will continue to play a central role in driving performance and efficiency to new heights.
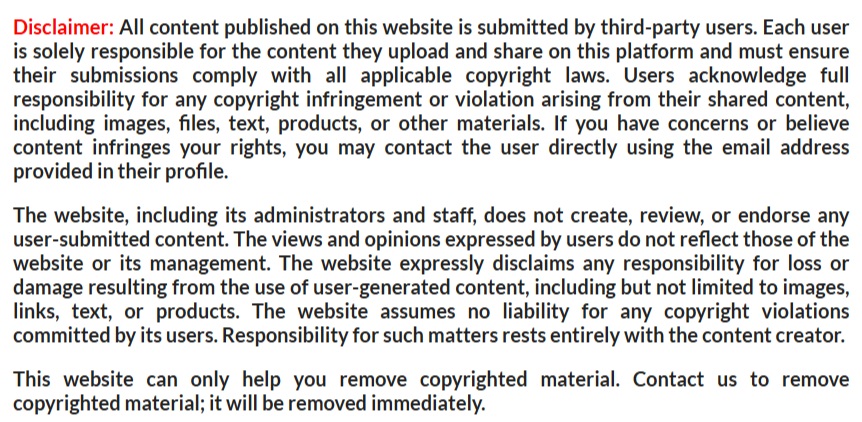